The evolution of our experience, attention to quality, and our unrelenting quest for Client Satisfaction are the fundamental ingredients, which have made ASTREA CLAIM SOLUTIONS develop their programs to such a competitive level, as regards the services offered
Features of the Service and how it is supplied
ASTREA Claim Solutions, being a Leading company in the market sector, offers highly competitive services to its Clients, regarding control of the whole supply chain and relative logistics. These highly specialized services require specific technical skills, constantly updated based on the different standards requested.
The high standard of services offered and their particularly tailor-made nature requires a precise description limited to the work stage the service relates to
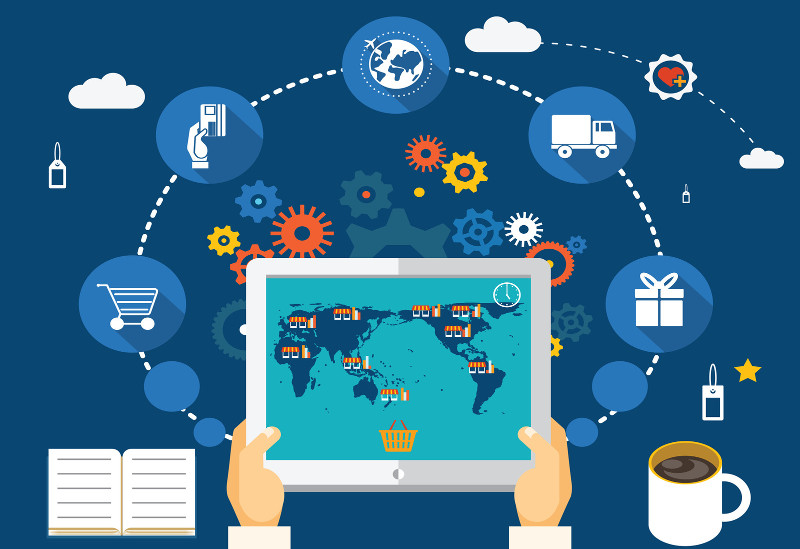
SUPPLY CHAIN SERVICES
Inspections, surveys and checks on goods which are yet to be channeled for retail, whose responsibility may be the manufacturer’s , the carrier’s, or of the Logistic Operators.
Specific checks are performed at manufacturing plants, at the hand-over stage, by compound management, logistic operator or receiver, in full compliance with the inspection standards required by the Manufacturer. The service is aimed at detecting and recording any damage or anomalies regarding production or assembly. This is the ideal tool to raise product quality, being able to highlight any production issues or recurrent faults.
Product verification can be extended to subsequent stages of transport, during hand-over between land and/or sea carriers. Checks are performed in compliance with tolerances and rules established in the Inspection Standards agreed with the Client: suitable documentation is issued to safeguard the Client from unjustified transport damage responsibility.
The inspections are performed at the time and place of loading/unloading agreed contractually with the Client (Pre-load e Post-Discharge inspection) aimed at certifying the real conditions of the product during handover.
Audits can also be arranged, anywhere along the logistic chain, aimed at detecting any possible technical or operative issue, or the non-respect of the agreed procedures during transport or storage of the product.
To clarify, Inspection services in Compounds and along the Supply Chain can acquire specific technical features based on the different sectors of operation (i.e. Automotive, Goods, etc.), for which documentation has been issued for each.
GREEN LEAN FACTORY
Mapping, analysis and process re-engineering are the principal features of the” Lean company” whose hallmark is extensive optimization of its strategic processes.
ASTREA CLAIM SOLUTIONS offers an Intervention Plan to be fulfilled using typical Lean Production methods designed overall to achieve “excellent” performance.
Lean Production, born from the Japanese automotive sector, in founded on the principle of production rationalization and production line efficiency, which cause significant waste reduction in terms of:
-
Less use of warehouse stock, with supply that adapts to demand in real time
-
Lower stockpiles of unfinished/unworked products
-
Reduction in throughput time
By applying ‘lean’ logic the company can supply waste-free products/services and consequently Value: starting from the process, by means of a balance for production capacity, work in progress and cycle times, it is possible to get a continuous flow of operations adapted to the final market, hence eliminating Non Value activities.
Increased efficiency in the production process also means rational use of energy resources which, in manufacturing industry, is if primary relevance. To this end ASTREA CLAIM SOLUTIONS‘ package includes checking and certification of the energy resources used, focusing particularly on renewable sources.
DEALER GREEN SERVICE
ASTREA CLAIM SOLUTIONS has developed a program aimed at defining and establishing an integrated evaluation system to monitor and rate the eco-friendly competitive capacity of its Dealer network in order to single out any possible technical/organizational actions for innovation.
The system is particularly useful for large companies which use a wide network of dealers which have to be qualified and monitored over time. The objective established is basically to create an efficient and flexible satellite activity which guarantees product and service quality through correct and unvarying management of company processes through adaptation to the Client’s defined standards.
The service boasts special environmental connotations: our intention is to offer small firms, who often do not have employees specialized in environmental legislation, the support necessary to find their way in such a complex and continually evolving subject such as environmental protection.
To complement this process, personnel training can be included, to guarantee development of a company “culture” based on Quality, destined become a strong point of the Company.
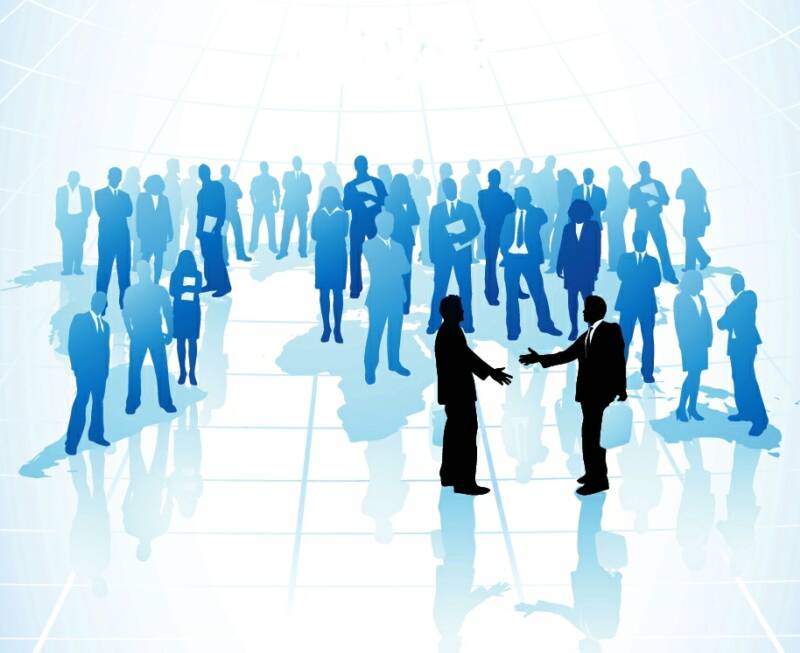
MANUFACTURING INSPECTION SERVICE
ASTREA CLAIM SOLUTIONS, using its own technicians and specific knowhow, supplies a top-level supplies checking and inspection service, in compliance with the requested quality standards.
The evaluation model is applied to suppliers of products, which have direct repercussions on the quality of the goods marketed by the Client.
The service can include planned or random checks performed by specialized staff, at production-line end at the manufacturing Plant, or at reception of the component at the Client’s premises, after transport.
The aspects to be checked are:
-
quality
-
product compliance and correspondence to contractual standards
-
defects and damage
-
correctness of labelling
-
suitability and intactness of packaging
An innovative computerized management system allows anomalies to be traced. If the Client requires it, its own IT tools can be used to operate with.
ASTREA CLAIM SOLUTIONS has devised Company Programs aimed at aligning Supplier Performance.
Based on the Client’s requirements, provisions are defined which suppliers have to adhere to in order to keep the acquired order, and its relative evaluation criteria. The system targets supplier’s compliance with the technical specifications of their product, timing and means of delivery.
Evaluation of suppliers’ behaviour which comes to light from the analysis described, will allow the establishment of a valuable improvement plan for the Client -an essential means of evaluating whether to maintain/increase/cancel the order. For the supplier it will be an indispensable tool for monitoring its own performance and the potential for increasing it.